By Amy Hedrick, CEO/Founder, Cleanbox Technology
In designing a UV-C-based product for multi-material, multi-dimensional surface decontamination, there are several critical components to consider. These components include the size of the objects being decontaminated, the complication of the surface structure of those objects and the various means by which UV-C efficacy can be maximized for targeted purposes.
Factors in Design
Having expertise in early design engineering using UV-C LEDs for targeted surface decontamination, the author’s company utilizes all the core elements of cumulative dosage design. As UV-C form factor capabilities continue to evolve, specifically in LED output, there remains ample opportunity for innovation for product manufacturers.
How does one design for maximum efficiency? Many things will impact this answer, including the engineering behind the UV-C product itself and the intended targeted surfaces of objects intended for decontamination. The total time of decontamination also should be considered when determining choice of UV-C output, as well as what matters to the target customer – coverage, time, impact on materials or other factors. Ideal dosage should not damage the surfaces being decontaminated, and care should be taken when choosing wavelength, form factor, reflectivity, exposure time and overall cumulative dosage.
Other limitations of UV-C engineering aside, one of the most frequently attempted method of expanding UV exposure – presumably with the goal of increasing efficacy – is the integration of reflective materials into a UV enclosure. Is reflectivity meant to extend the reach of the light to areas beyond its natural reach, restricted by placement of UV-C in proximity to the overall design of the product? Is it meant to increase what adequately can be decontaminated in the unit? Or is the reflectivity intended to increase intensity of dosage on already exposed surfaces? The choice of UV-C form factor and subsequent cumulative dosage could impact the decision to consider reflectivity in the design. The author’s company has found that exploring reflectivity in product design has been a useful exercise.
Of course, a perfectly engineered product might not be manufacturable at scale for a specific business or cost effective for the market. At the same time, the general population is starting to see a plethora of “UV boxes” being marketed directly to them as “effective for decontamination,” based solely on the fact that the boxes have a source of UV light and some mirrored or reflective surface.
Experimental
The author’s company looked at the impact of a number of reflective products, with a focus on results in the 265 to 275 nw wavelengths (LEDs only), as its products have targeted surface decontamination for even, overlapping light coverage with dosage that considers limits to avoid overexposure. The engineering team selected 10 variance surface and material types to measure reflectivity, as well as for general comparison purposes. Some materials and surfaces were not expected to provide significant reflectivity but were included for benchmark comparisons. The materials tested were:
- Black Powder-Coated Aluminum (as a control standard)
- PTFE Liner
- Anomet UV-C Diffuse Aluminum Anodized Reflector
- Aluminum Adhesive
- Clear Acrylic
- PTFE Coated Fiberglass Fabric
- ePTFE Coated Fiberglass Mesh
- ePTFE Membrane
- ePTFE Gasket
- Reinforced PET Liner
The measurements were performed on a Perkin-Elmer Lambda 9/19 UV-Vis-NIR Spectrometer with a LabSphere Reflectance Accessory RSA-PE-19 in 8°/Hemispherical Reflectance Factor geometry; traceable via ASTM Test Method E1331-96 , E903-96; NIST SRM 1920; SRM 2035; SRM 2036. Each sample was placed at the aperture of the integrating sphere inside the instrument
Exposure Times: 2+ minutes
Approximate DTS Ratio: Each sample was placed at the aperture of the integrating sphere inside the instrument. Results are summarized in Chart 1.
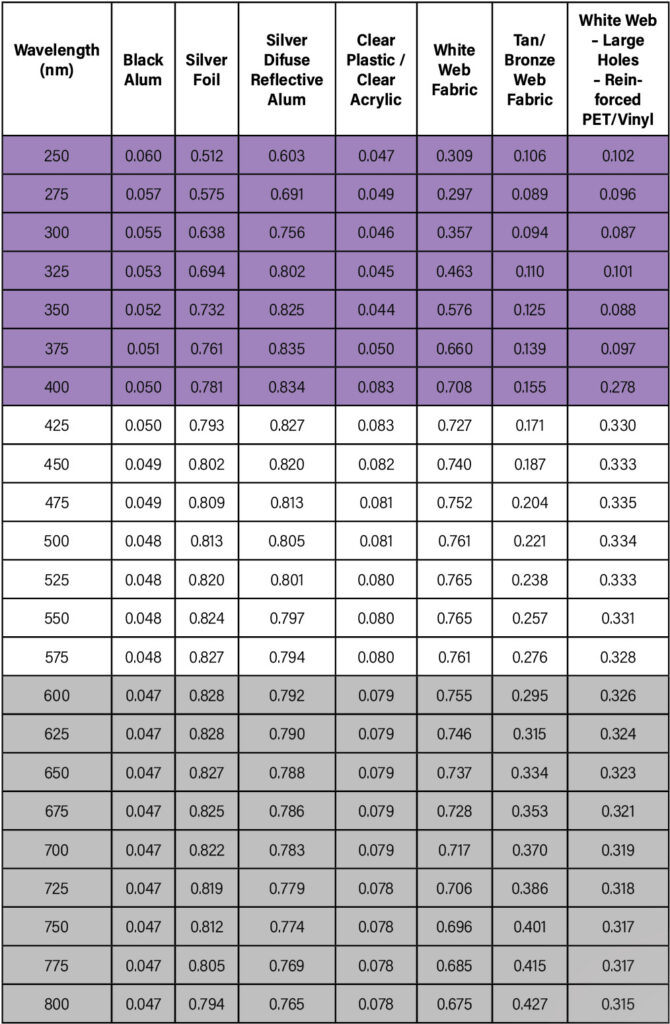
Comparison of Reflective Products
Materials such as powder-coated treated black aluminum were found to be in line with expected results and maintained almost the same amount of reflectivity across the entire spectrum of 250 to 800 nm, with slight measurable but non-impactful increases in reflectivity at the lowest wavelengths. Silver foil-coated aluminum had five times the reflectivity when compared to black powder-coated aluminum between 250 to 275 nm, with an approximate 12% spike in reflectivity around 350 nm. A porous coated fabric consistently showed double the reflectivity of black-coated aluminum across the spectrum, with an uptick by 8 to 10% at 325 nm. The sample was an EPTFE-coated fabric that was used for comparative testing against a PTFE-coated fabric.
Not unexpectedly, various PTFE, EPTFE and other membranous materials at a range of thicknesses showed the highest reflectivity of 90% at 250 nm, with little variation. For example, PTFE .5mm had 92% reflectivity at 275 nm, with the best reflectivity of 93% starting at 350 nm. EPTFE filter membrane was close in reflectivity to PTFE, dependent on thickness and other considerations. The engineering team chose not to test mirror reflection because mirrors are coated with glass; it was assumed polished aluminum would reflect slightly better results.
Samples showed immediate reflectivity, but the refractive impact of having multiple sides covered was not tested. PTFE and EPTFE are both considered diffuse reflection materials of UV and, no matter the direction, the light scatters highly reflectively and evenly. However, fundamentally, light dispersion within an enclosure will be impacted by angles of the enclosure and where the reflective material is applied.
What this means in terms of product efficacy will depend on many factors that the designer should consider when in the engineering stage. Increased reflectivity is only as “effective” as the cumulative dosage and exposure determined by the design of the product. Ultimately, these tests measured reflectivity, which is not indicative of efficacy or dosage, although – depending on use – may contribute to one or both. When considering reflective materials from a product-development standpoint, a number of other factors will be taken into consideration.
Conclusion
Materials that have reinforcing elements may have UV absorbance up to a certain point, after which they may have some UV reflecting properties. Ultimately, when designing a product for decontamination, no single test will determine the ultimate efficacy of the product. The final development decisions likely will be based on a combination of factors that determine cumulative dosage, price point and manufacturing capability.