By Liz Stevens, writer, UV Solutions
Data centers, which are popping up everywhere to handle the exploding use of computational power, are getting some good press for efforts to make them more sustainable. Data centers generate a huge amount of heat – generally as hot air or hot water – which often is wasted. There are many innovative re-uses of the heat: piping hot air from data centers to nearby greenhouses is one re-use; directing hot air or hot water to district heating systems is another. In Japan, a data center sends the warmed water from its cooling system to an eel farm, keeping the sushi-bound eels healthy until harvest.
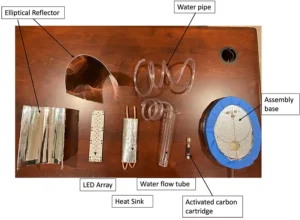
Data centers, however, aren’t the only ones doing creative things with heat, energy and water. A novel use of heat generated by a water disinfection lamp and the cooling power of the water being disinfected have been developed in conjunction with a UV water disinfection treatment process.
Sudhish Swain and his collaborator, Aadi Gannavaram, then students at Montgomery Blair High School, Silver Spring, Maryland, presented the poster “Designing a cost-effective and high-throughput water purification system utilizing UV-A LED technology” at the 2023 IUVA World Congress in Dubai, UAE. The poster displayed info on Swain and Gannavaram’s design of a system utilizing UV-A (not UV-C) LEDs, which includes out-of-the-box ideas for addressing the challenge of providing safe water for the world’s population. Swain, now a freshman at Harvard College, gave UV Solutions insight into the project.
Developing the Prototype
While conventional water disinfection systems use physicochemical methods and UV-C irradiation, that technology has high costs, low device lifetimes and environmental downsides due to the use of low-pressure mercury arc lamps. Swain and Gannavaram sought out alternatives. Swain described the impetus for developing this system. “My past research exposed me to a synergy potential – that heating water to 37° C will allow it to be disinfected with UV-A light,” he explained. “I wanted to use UV-A instead of UV-C to tap some of its unique strengths, so I decided to overdrive the LEDs and generate more heat – which I can harness to heat the water to the optimal temperature – and also to get more UV output.”
The new system generated a UV-A energy output of 25 J/cm2 by applying a higher current than normal to the UV LEDs. The heat byproduct of overdriving the LEDs is captured by the water, raising its temperature to 35° C. “The synergy between intense UV-A radiation and the now-heated water,” Swain explained, “is used to disinfect the contaminated water to the same efficacy as UV-C irradiation.” Their prototype demonstrated up to 1 Liter/min of water purification and > 5 log reduction in microbial load.
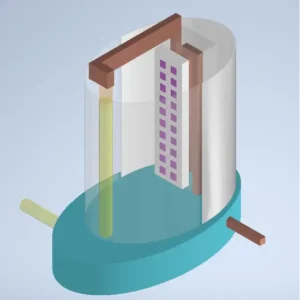
“While UV-A comes in 365, 385, 395 and 405 nm normally,” said Swain, “we settled on 365 nm and 395 nm in this project; those are the most commonly used wavelengths in the industry and readily available to us.” Swain cited advantages of using UV-A over UV-C. “UV-A’s unique strengths are that it is safer, more electrically efficient, has a longer lifetime and is less expensive. It also has a fundamentally different way of removing microbial pathogens,” he said. “Unlike UV-C, which breaks the DNA bonds, UV-A in conjunction with heat causes the production of reactive oxidative species – which does not allow for photoreactivation of the pathogens. UV-C, on the other hand, allows for the regrowth of pathogens under certain conditions, leading purified water to have a ‘shelf life’ when it has been treated by UV-C.” (The system includes an activated carbon filter in the front end of the treatment train so that input water goes through a physical and chemical filtration process before the UV disinfection.)
In applying higher than normal electrical current to the UV-A LEDs, Swain and Gannavaram proceeded carefully. “Our LED board was on a metal core PCB directly bonded to a heat sink,” Swain said. “We had a driver, driver electronics and a suggestion from the LED manufacturer for optimal amp/volt (3.3 V and 250 mA).” Because they wanted to overdrive the LEDs, they worked with an electrical engineering team to design a driver that could drive much higher current into the LEDs (3x overdrive, 750 mA). Constant voltage was maintained at 3.3 V and the overdriven current was 750-800 mA.
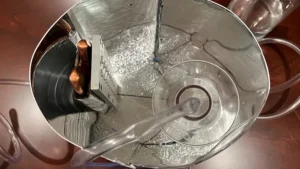
These types of modifications might have compromised the warranty coverage of the LEDs or their working life, but Swain and Gannavaram had those contingencies covered. “Typically, higher current would compromise the warranty,” said Swain, “but there is a critical parameter in LEDs called junction temperature.” He explained that as additional current is applied, the junction temperature increases. “The beauty of our design,” Swain said, “was that we were using the same water we were purifying (very good coolant) to cool our LEDs, and this allowed us to keep the junction temperature around 40o C, well under the manufacturer’s suggested 60o threshold.” In general, for every 10 degrees an LED is heated above that threshold, the lifetime of the LED decreases by half. “Our cooling method,” said Swain, “mitigated that problem so that using a higher current does not affect the lifetime of the LEDs.” For this project, the expected lifetime is about 20,000 hours; after running for 20,000 hours, LED intensity drops to 70% of the original value. “We always assumed the worst-case LED output in our design when considering the reactive oxidative species,” Swain said. “Even with 70% of the peak intensity, we still could generate the reactive oxidative species.”
The technology has earned an approving nod from Sunil Kumar, director of Central Water Commission, Government of India, New Delhi, who reviewed the system and technology “for developing countries like India, which has a maximum number of waterborne disease patients. In such scenarios, the innovation by YUV-Aqua (Swain and Gannavaram’s start-up company name) on the basis of UV-A technology proposes a potentially viable solution to such problems.”
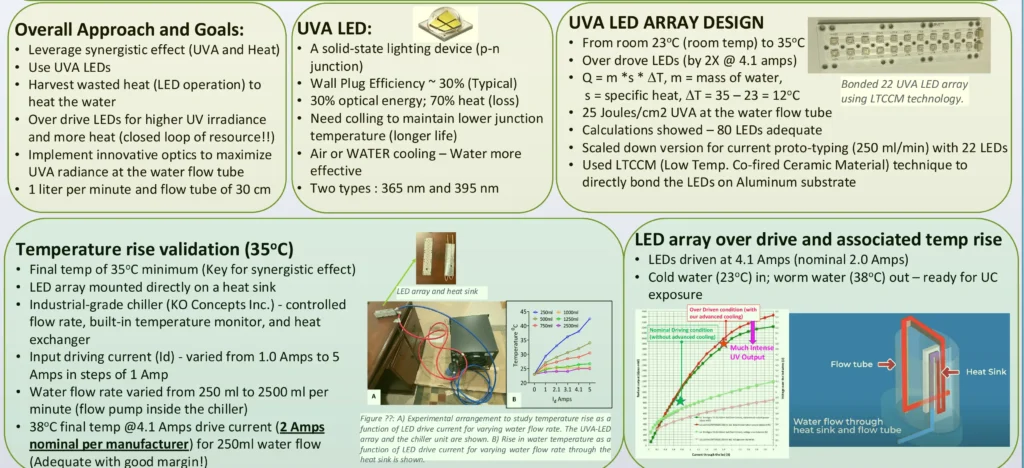
The Next Steps in Design
As a result of this project, Swain and Gannavaram have filed patents for the technology and are improving the design and developing prototypes with seed funding from friends and family. “For our next design,” said Swain, “we have added sensors and controls to ensure that when the water enters the UV irradiance tube, it is guaranteed to be 37o C. And in the new design, we are not completely relying on overdriving LEDs to heat the water; we added a heating filament, like you would find in a coffee machine, to ensure the water is heated up to the desired temperature within a few seconds. This will help us deal with different input temperatures of the water during different seasons.”
Reduce, re-use, recycle. Swain and Gannavaram have charted a new path for using the thermal energy byproduct of UV-C LEDs to heat water for disinfection, meanwhile using the very water being disinfected to cool the UV-C energy source. Very circular.
Swain plans to major in biology with a secondary major in computer science or math at Harvard. He hopes to enter the field of biotechnology and pharmaceuticals. Gannavaram currently is a senior at Montgomery Blair High School.
For more information, email sudhishmswain@gmail.com and visit www.steminlife.com/stem-projects/water-purification-projects.