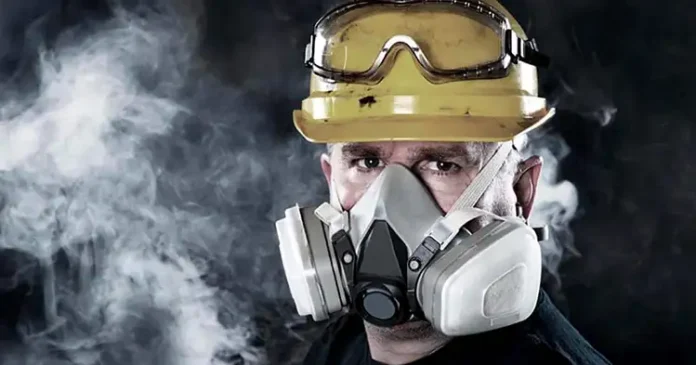
Castine A. Bernardy, Ph.D. Student, Civil and Environmental Engineering, University of New Hampshire
James P. Malley Jr., Ph.D., Editor-in-Chief, UV Solutions and Professor of Civil and Environmental Engineering, Department of Civil and Environmental Engineering
Planning for this edition of Operator’s Corner focused on safety advice from municipal systems that treat drinking water, wastewater and water for reuse, including systems that use the combination of UV and hydrogen peroxide to form an AOP. There were 10 respondents, and one of the respondents sent a quote from a paper by Borchers et al. 2008, copied here.
Question 1. What safety training is provided to operators specifically related to the UV system, and who is responsible for providing it?
- All respondents indicated that initial safety training was provided by UV equipment providers or their representatives. Five respondents indicated that their health and safety programs provide annual training updates on all related aspects of operations. Two indicated that their operators were receiving the necessary updates and credits from professional organizations, such as NEWWA, NEWEA, AWWA and WEF.
- All respondents indicated that they felt the most crucial training was on lock out/tag out and discharge of capacitance before working on UV-related systems.
- Four utilities noted that their operators were trained in chemical handling and safety to use the acid and base cleaning chemicals used to clean the banks and racks of their UV lamps.
Three utilities mentioned the challenges of dealing with high-strength hydrogen peroxide and how their operators need specific training to deal with this aggressive chemical and to avoid risks of fire and explosion. - Three utilities mentioned wastewater channels and training their operators to access these confined spaces since they had frequent need to do that to fix valves and UV banks of lamps.
- Nine utilities mentioned concerns regarding the handling, clean-up and disposal of mercury-containing lamps, especially when breakage occurs. Only one utility mentioned online breakage and issues with that, while all others mentioned breakage during lamp handling and replacement. The utility with online breakage experience emphasized the importance of respiratory protection during handling and clean-up when a mercury-containing lamp is broken. This respondent attached the following key sentences from an IUVA News article (Vol. 10, No. 1, 2008), with quotes from Borchers et. al:
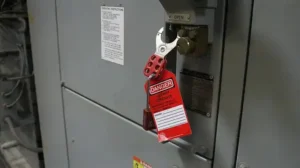
“This paper focuses on examining the risks associated with online lamp breaks in ultraviolet light (UV) drinking water treatment facilities. UV lamps generate UV light through the vaporization of elemental mercury, by using energy through temperature and pressure to drive the mercury into a vapor phase. Mercury is a heavy metal and is regulated in drinking water by the United States Environmental Protection Agency (USEPA) through the Safe Drinking Water Act (SDWA). If an online lamp break did occur, and mercury was released, techniques such as dilution or treatments must be employed to ensure that the resulting concentrations in the drinking water are maintained lower than that of the Maximum Contaminant Level (MCL), which is 0.002 mg/L as set by the USEPA. Research conducted by the USEPA, and others reveals many unique properties that the element mercury demonstrates. This research also aided in pinpointing the potential risks to both water consumers and UV treatment facility operators. In many cases, the risk of inhalation of vapor phase mercury by treatment plant personnel responsible for accessing the mercury released and conducting clean-up activities is the most significant concern that needs to be addressed. For many water systems, the dilution achieved by the flow rates being treated or by the downstream volume provided by the clear well or distribution system piping will ensure that the mercury concentration reaching the public is well below the MCL and often reaches non-detectable levels. In smaller systems, where adequate dilution may not occur, other operational controls and treatments may be necessary to ensure the risk of ingestion of mercury from the contaminated water is alleviated.”
Question 2. Are there recommendations for ways to improve the safety of UV facilities that can be shared with other operators?
- One utility volunteered that a minimum of two operators are required to be involved on all tasks since this buddy system is much safer. One operator performs the task and signs off, and the other operator is required to check the task and sign off on it.
- Two utilities indicated they have operators trained as licensed electricians who handle all aspects of UV repairs that involve the electrical components.
- Two utilities indicated they continue to look for ways to improve hydrogen-peroxide handling and actively are looking for alternatives to using that chemical, with one utility mentioning its staff was looking into UV and chlorine AOP options.
- Three utilities indicated their decision to upgrade and phase out lime-away chemical dip tanks has improved operator safety and reduced chemical mess.
- Two utilities urged UV Solutions [sic] to move away from so many lamps in modern designs and make them mercury-free.
- Three utilities indicated that operator time, attention and safety would be improved if problems with leaking isolation valves and water-level control valves could be corrected by improving valve quality or making channels that do not need valves at all.
- One utility asked for better UV technology monitoring software so that its SCADA systems would receive enough information for operators to take earlier action and head off problems, such as lamps getting dirty.