Castine Bernardy, Ph.D. student, Department of Civil and Environmental Engineering, University of New Hampshire
James P. Malley, Jr., Ph.D., editor-in-chief, UV Solutions, professor of civil and environmental engineering, Department of Civil and Environmental Engineering, University of New Hampshire
Editor’s Note: Owners and operators of UV technology are an important stakeholder group; these professionals have limited time and often prefer to remain anonymous when providing feedback. As a result, this column is built from responses to a Qualtrics survey sent out each quarter with the help of UNH graduate students.
Major events, while often disruptive or tragic, spur reactions that can lead to positive outcomes. The COVID-19 pandemic is viewed by many as one of the most globally impactful events since World War II. One of the positive outcomes has been an unprecedented increase in research, development and engineering applications of UV technologies. UV technologists have not seen an increase in activity this large since the ’90s when a waterborne disease outbreak from Cryptosporidium sparked decades of UV technological growth in the water field and led to the birth of the IUVA. The objective of this column is two-fold: Report lessons learned from the application of UV technology to water, and suggest ways those lessons can inform the next steps in the selection, design, application and monitoring of new UV disinfection systems for air and/or surfaces. The survey asked the following three questions:
How do operators know their UV facility is working?
A respondent from a large drinking water plant replied, “Each month we produce a state report ensuring that our UV system operates in specification and achieves the objective of maintaining 2-log disinfection credit for Giardia and Crypto at least 95% of the time – although we generally hit 99%.”
A wastewater facility representative responded with, “Our daily samples are used to determine our average monthly E. coli count, and if we are at 14 CFU/mL or less, we meet our discharge permit.” A response from an innovative and recently built application of UV disinfection in drinking water stated, “We worked with our two consulting engineers, the UV maker, the state and UNH researchers on our EPA pilot study to obtain 3-log virus credit for UV. We monitor flow, UVT and delivered UV dose continuously and report it monthly to the state to demonstrate compliance and on-spec operations. We are on spec more than 97% of the time, and our past problems with low source water UVT have not reoccurred.”
Ensuring public safety and device efficacy for the air and surface applications of UV technology for the foreseeable future likely will be much more difficult. In the absence of clear regulatory guidance and standards, the purchaser and/or operator of the UV technology – as well as the public it is meant to protect – are left without a uniform, STEM-based proof of performance.
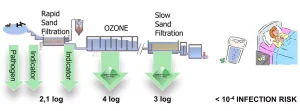
Several members of the UV technology community, including IUVA President Ron Hoffman, have suggested the adoption of a Quantitative Microbial Risk Assessment (QMRA) approach (Figure 1). A QMRA type approach provides a uniform basis for the current US drinking water regulations (Figure 2), which specify that disinfection technologies must provide a 4-log virus inactivation capability (credit). The QMRA calculations followed this basic logic:
- Risk set at one new infection per 10,000 exposures.
- Infectious dose set at < one virus particle per exposure.
- Initial virus concentration assumed 10,000 #/volume.
- Calculated regulatory requirement: Log (10,000) – log (1) ~ 4-log inactivation (US drinking water law).
What lessons were learned from applying UV technology?
A respondent at a wastewater facility with 30 years of experience suggested the importance of “checking with other places that bought and use the UV system you plan to put in. Be sure the system has enough dosing capacity to deal with unexpected pathogen loads. We are on our second UV system, replacing the first one after 15 years of problems. It was ineffective, claims made were wrong, lamp replacement was too frequent and the sensors never worked. (We just turned them off.)
“My men spent a lot of time fixing components in that system; the town hired an electrical guy just to deal with it each day. The new equipment has been running for approximately 16 years and has been very good, as it uses a lot less power and labor. It uses wipers, and with our upgraded I&C in 2016 we can monitor it using Wi-Fi or cellphone from anywhere. I think the old one had over 200 coliform violations; the replacement system has less than one in a year.”
Owners and operators also offered comments on improvements they have seen over the years regarding the shift from low-pressure (LP) mercury vapor lamps to medium-pressure (MP) lamps and, most recently, to the balancing of fewer lamps with more energy efficiency that gave rise to low-pressure high-output (LPHO) lamps. “The first systems we used at the W1 had shorter lamp life than expected, and we had to maintain a large number of lamps and much more electrical maintenance. When we built UV at W2, I installed MP with about 10 times fewer lamps, making it much easier to keep them clean, and we had almost no electrical fixes. However, it used a lot more power and had many ballast problems for the first few months. We put out a bid for a new UV system to replace W1 and cities’ focus during the bid was to require components meet applicable certifications and the entire system meet EPA validation in addition. We want maximum energy efficiency, longer lamp life and much less maintenance cost.”
The recent UV LED literature for drinking water suggests that technology is progressing, as demonstrated by the article published in Q3 2019 on the Typhon UV LED system validated by Carollo Engineers using the EPA Ultraviolet Disinfection Guidance Manual protocols up to a flowrate of 250 m3/hr (~1.3 MGD).
This promising validation result, at a larger scale than seen before, will undoubtedly promote next steps and the actual field use and benchmarking of UV LEDs in small drinking water system flow applications. It is hoped that owner/operator experiences with the more conventional UV lamp technologies can inform the emerging applications of UV LED in water disinfection.
Scale up and benchmarking lessons learned in the UV applications for water can provide a valuable resource to the process engineering needed for air and surface disinfection. The water experience suggests due diligence, importance of conservative design, as well as validating system components and overall system performance. We look forward to the day when owners and operators of UV facilities for disinfection of air and surfaces on a larger scale can provide feedback, lessons learned and benchmarking of those applications.
Water UV owners and operators also offered comments on the changes they have seen in lamp systems. “We started in the ’90s with many low-power LP lamps at three wellhouses, which were a headache to maintain. By shifting to MP lamps, we saved space, used autowiping and had much fewer electrical connection problems. Our five-year plan to reduce carbon footprint includes a switch to LPHO systems.”
As process engineers focus on UV applications for air and surfaces, they should consider the advantages of fewer, more energy-efficient lamps to reduce operation and maintenance issues as well as embrace the continuing efforts to reduce carbon footprint.
What monitoring of the UV facility is performed and/or required?
Water UV systems include certified components, validated process performance and the governing principle that if a potential aspect of a UV system – such as low wavelengths from an MP lamp – cannot be monitored, then it cannot receive disinfection credit. Effective monitoring relates on a day-to-day basis, to the key question: Did I get what I paid for?
An ASDWA member responded to this question with good insight: “Overseeing four MP systems, we struggled with the best way to correct for low wavelengths and quickly adopted a policy that if calibrated and verified low-wavelength sensors are not used, then disinfection credit for these wavelengths cannot be given, and the validated operating flows of the treatment plant need to be reduced. It helped us to have independent third-party guidance from consulting engineers and UV experts recommended by IUVA.”
Furthermore: “Each reactor has a human-machine interface (HMI), and they monitor the UV systems and dump continuous data to SCADA on flow, UV sensors, influent UVT monitors, calculated UV dose, all alarms, hours of lamp operation and reminds us when UV sensors need to be checked against our reference sensor. Everything is backed up at the end of each shift.”

Water UV technologists and process engineers have wrestled with this monitoring question in drinking water since the early 2000s. Since 2006, drinking water facilities across the US have addressed this question by providing independent third-party-validated UV systems, validated sensors (germicidal and low wavelength as appropriate) and essentially continuous monitoring of key parameters to ensure the UV technology operates within the validated range (corresponding to flow, UV transmittance of the water and lamp sensor reading) and the owner and the public are getting what they expected. Example displays from typical HMIs on UV devices depicting parameters continuously monitored are shown in Figure 3.
Some version of this approach can be refined and adapted so that the promise of widespread UV LED use in water applications can be realized. For example, when a reactor is composed of hundreds and/or thousands of individual UV LEDs, a means of effectively monitoring this system on essentially a continuous basis will need to be devised so it can monitor and respond to aging, fouling or changes in flow or UVT of the treated water.
Applications of UV technology to air and surfaces may benefit from water UV experiences and improvements in monitoring and process control. Historically, the efficacy of UV applications for air and/or surface disinfection for controlling measles, tuberculosis or, more recently, reducing healthcare acquired infections (HAIs) at the full scale have been anecdotal in large part, backed up by a few well-designed studies that collected data and then inferred a logical cause and effect between installing UV treatment as part of a multifaceted approach for disease control and the rates of infection.
If widespread application of UV to air and/or surfaces need to demonstrate that benefits outweigh costs (which may include known or unknown risks) it is likely that owners and operators will begin to expect more specific monitoring and control data to be collected and reported.
Contact: Castine Bernardy, cab2020@wildcats.unh.edu; James P. Malley, Jr., jim.malley@unh.edu